Fluid 4.0 - Implementation of digitalization for fluid power technology 4.0 using asset administration shells, submodels and demonstrators
In the Fluid 4.0 project, fluid technology manufacturers, machine and system manufacturers, users and service providers are working together to solve digitalization issues. Specific use cases and general challenges in fluid power technology are being addressed.
Fluidon GmbH is actively involved in this project by contributing its extensive expertise in the simulation of fluid power systems. Fluidon is developing an I4.0-compliant simulation solution and the infrastructure for integrated and digital engineering of fluid power systems.
The challenge of engineering fluid power systems
Fluid power technology, including its hydraulics and pneumatics branches, has an annual turnover of around 9.6 billion euros in Germany, with an export ratio of around 60%. Fluid power technology products are characterized by their high flexibility, dynamics, reliability, robustness, long service life and high power density with comparatively low weight. For this reason, fluid power products are widely used in almost all areas of mechanical engineering as crucial components in both stationary and mobile systems.
The wide range of variants and flexibility of use of fluid power components generate a large amount of data and information, which is the key to future value chains. Fluid technology manufacturers as well as machine and plant manufacturers (OEMs), users and service providers are dependent on this information throughout the entire product life cycle. In this context, digitalization efforts and initiatives in the area of "Industry 4.0" are seen as the pioneering path to the future of the industry. This approach not only enables efficiency and production increases, but also creates space for the development of new business models with both economic and ecological benefits for OEMs and their customers.
Digitalization in the context of Industry 4.0 and the cross-manufacturer exchange of data and information are bringing about a fundamental change in the entire value creation system. As a supplier industry, fluid power technology faces particular challenges in this regard due to its application-specific combination options and the broad spectrum of its applications.
In contrast to other industries, only a few standardized application scenarios or units with predefined inputs and outputs can be created in fluid power technology. In order to do justice to this diversity in the context of digitalization, the VDMA Fluid Power Technology Association and its member companies have agreed on a digitalization concept. This concept offers maximum flexibility and compatibility with other formats such as OPC UA or Automation ML by implementing the digital fluid power twin, which is generated using the Asset Administration Shell (AAS).
The aim is to improve cooperation and interaction between fluid technology manufacturers, machine and system builders, users and service providers. In future, manufacturers will be able to supply their physical components together with asset administration shells to their customers, especially machine and plant manufacturers. The latter can use the digital twin of the components for their data-driven processes and applications, which ensures an efficient and transparent solution for data management in Industry 4.0.
Project consortium
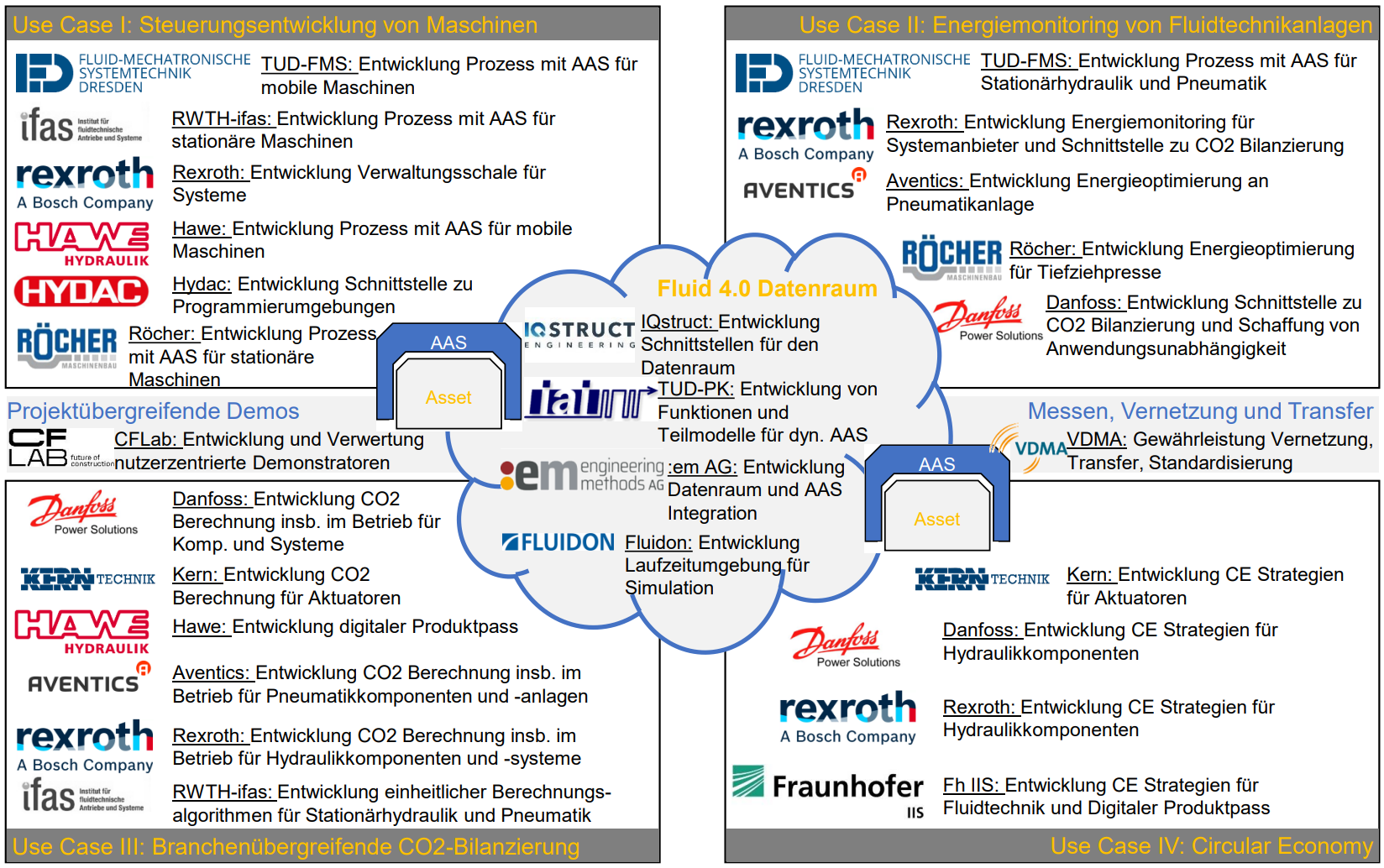
With the aim of addressing the current deficits and challenges in relation to the digitalization of fluid power technology, a consortium has come together to work on the following key areas:
- Approaches for cross-industry, machine-readable data provision for fluid power systems (data room for fluid power technology)
- Higher-level asset administration shells at system level that intelligently link the already well-developed infrastructure at component level
- Domain-specific services for fluid power technology applications
- Digitalized interfaces between manufacturers and users as well as to other data standards, digitalization technologies and engineering tools
- A cross-life cycle determination of CO2 emissions and circular economy concepts for fluid power technology
- Integrated digital engineering at the level of fluid power components
Work program
FLUIDON is concentrating on the following key areas as part of the project:
- We integrate the simulation models into the I4.0-compliant data space.
- We design the system administration shells for the intelligent connection of component simulation models to an overall system simulation.
- We are developing an I4.0-compliant simulation solution and infrastructure as the basis for various services in fluid power technology applications.
- The resulting solution enables the seamless integration of simulation-based engineering methods without data consistency breaks with conventional methods.
- We support our partners in implementing simulation-based services in the emerging I4.0-compliant simulation framework.
- We develop a solution for system simulation that is numerically stable and powerful (FMI co-simulation).
- The simulation interface, which we are designing on the basis of the asset administration shell, enables interoperable access to data from the simulation.
- We use an application example to demonstrate simulation-based control system development.
- We calculate the energy consumption of the components during operation to balance the CO2 footprint.